The universal multiprocessor contouring control for milling / turning / grinding / positioning. The continuously further developed control generation of the F / D / S series complements Engelhardt's product range in the low-cost sector. Compact, convenient and cost-effective were the requirements that were achieved through consistent miniaturization and a high level of component integration.
The complete CNC control is housed in a 19″ wide housing with an installation depth of just 100 mm. It is suitable both for original equipment and for retrofitting conventional machine tools. Equipped with protection class IP 54, the large operating keypad and the graphic LC display are designed for tough workshop operation. An electronic handwheel with adjustable handwheel factor and a potentiometer for controlling the programmed feed rates are built into the front panel.
Various software versions (milling, turning, grinding and positioning) are available to the user. They include linear and circular interpolation, tool management and compensation, parametric programming, main spindle control, etc. as standard. There are also 16 I/O channels and two V 24 interfaces for data exchange. The connections for the keyboard and VGA monitor are led out. The control unit can therefore be located up to 10 m away from the control panel. Depending on the application, machining cycles such as contour turning, pocket milling etc. are integrated.
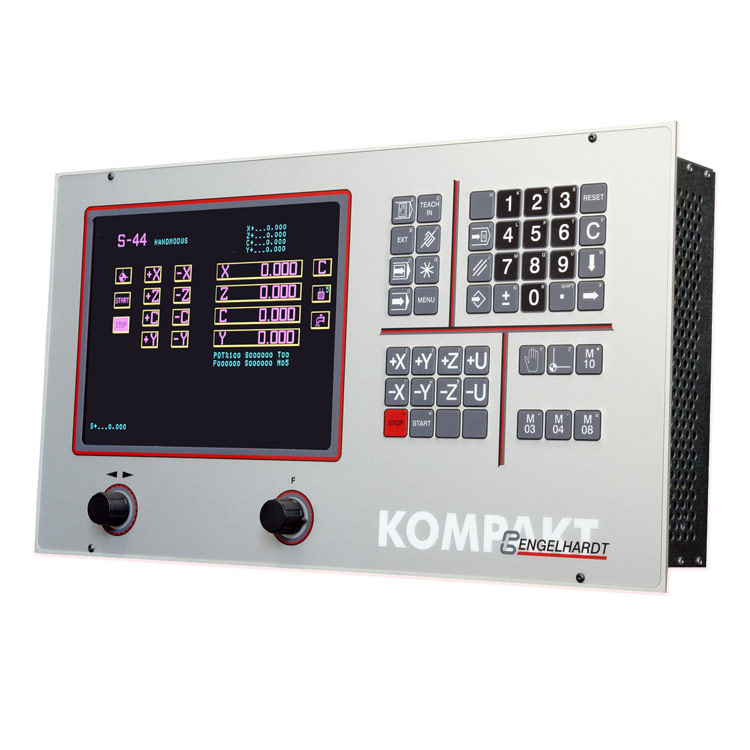
Programming is carried out in accordance with DIN 66025 (G and M functions) and is graphically supported on the screen. Thanks to the multiprocessor design, position controller cycle times of 200 µsec are achieved, guaranteeing a precise path and exact positioning. The F / D / S versions are equipped with outputs for servo motors.
Features |
---|
19″ 6U housing for front panel mounting. |
10″ Color - LCD |
Interpolator cycle time 2 msec |
Position controller cycle time 200 µsec |
High path and position accuracy |
Servo systems are easy to optimize (P-I-D value) using a curve monitor that graphically displays the setpoint and the position lag (difference between setpoint and actual value) on the screen |
Tachomat software prevents dynamic overloading of the mechanics by automatically reducing the feed speed |
Plain texts for instructions and value entries freely programmable |
Speed pre-control for drag distance minimization |
Up to 16 inputs and outputs in the CNC program |
Setting and resetting the outputs without stopping the axes |
Continuous driving with all drive types |
2*SSI interface for absolute encoder |
2 * V24 Interface: - For data backup and remote control - For the transfer of CAD/CAM data - For connecting an external hand-held control unit - For connecting an external USB interface |
Applications |
---|
You can find application examples from our partner companies under the following links: |
HPH Werkzeugschleiftechnik GmbH |
NCW155 |
NCW/AWS300CNC |
VARIOGRIND |
Technical data (dimensions incl. plug) | |
---|---|
Height | 268 mm |
Width | 483 mm |
Depth | 150 mm |
Downloads |
---|
Operating instructions and other documents for our control units can be found in the Downloads. |
Have we aroused your interest?
We would be happy to discuss your individual requirements for your project with you.
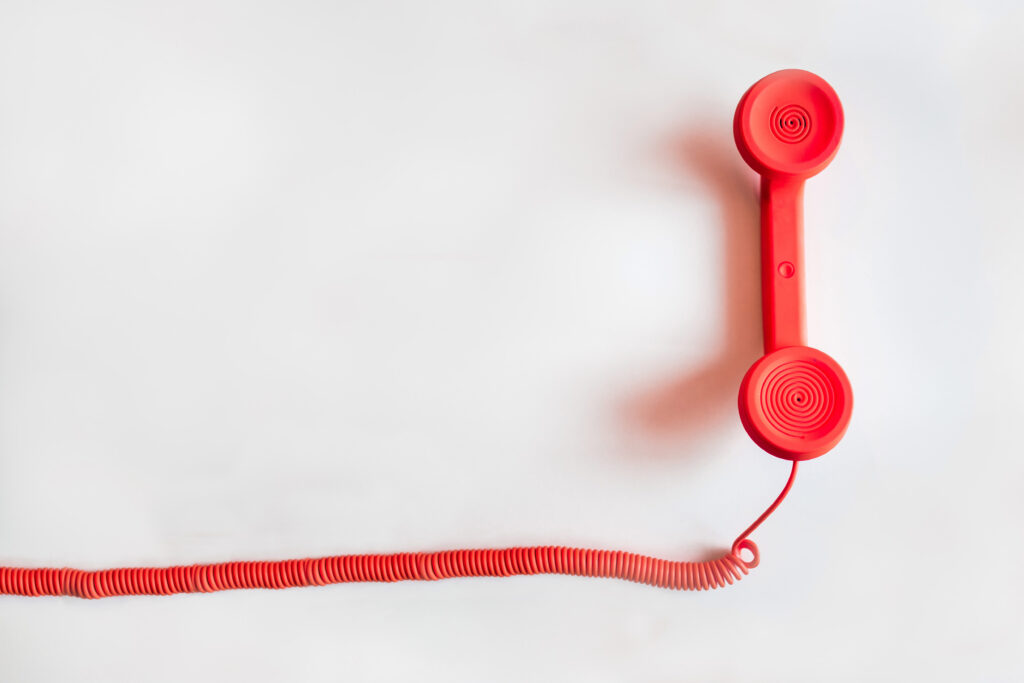